For many products and equipment, engineers should go with custom cylinders. It lets engineers “build” cylinders that fit the customers’ needs and eliminates the inherent inefficiencies of under- or over-engineering.
There are several key design aspects to keep in mind when specifying custom cylinders.
Each of these considerations presents a challenge for standard cylinders, but custom designs can overcome these challenges and turn them into opportunities for better cylinder performance. Considerations include:
Cylinder sizing. An inappropriately sized cylinder can have drastic implications for the performance, efficiency, and reliability of any hydraulic system. Cylinder barrel bore size is particularly important, as it determines the force the actuator can generate. If the cylinder diameter is too small, the actuator may not reach the customer’s targeted speeds or cycle times.
Rod choice. When choosing the best rod for a cylinder, its diameter and material type are important. The goal is to get the lowest priced rod that is suitable for the application at hand. By designing custom cylinders with fatigue, buckling and impact-failure in mind, engineers can design better, more efficient rods. This could help reduce the piston rod diameter which, in turn, lowers the cylinder’s weight and the price of the cylinder.
Custom cylinders and rods also let designers choose among several materials. Nitro steel shafting, for example, offers protection when applications involve consistent exposures to chemicals such as fertilizer. Induction hardened shafts can be used for its added protection, which exceeds that of than standard chrome when it comes to handling debris that may affect the shaft and lead to premature failure.
Seals. No single seal material and type is compatible with every cylinder design. Depending on the customer’s application, they can be made of elastomers, thermoplastics, or thermoplastic elastomers such as rubber, polyurethane and polytetrafluoroethylene. An application and its pressure, temperature, speed, and the environment must be taken into account to get the right custom seal.
Cylinder mounting, assembly and maintenance. Custom cylinders with orienting ports, manifolds and hoses/fittings designed with a specific application in mind can simplify assembly and setup. This saves time when installing the cylinder at a customer’s location. It also streamlines operations by making the cylinder more accessible for repairs and maintenance.
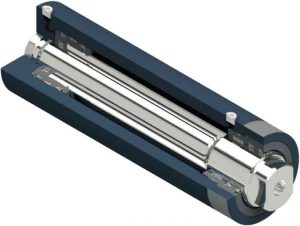