Hydraulic cylinders, jacks, or rams. The names vary but whatever you choose to call them the definition is the same. A hydraulic cylinder is a device that harnesses the pressure generated in a hydraulic system to move a load. Due to the wide variety of cylinder options to choose from, you will need to consider your needs carefully when selecting a cylinder for your job.
What stroke is required?
Related to the maximum collapsed height, is the stroke length required. Stroke is defined as the difference between the fully extended height and the fully retracted height of the cylinder. It’s the distance between the top of the plunger piston and the bottom of the stop ring. For jobs that need extra stroke, there are telescopic hydraulic cylinders including low-height versions. The stroke determines how far the cylinder will lift, push, pull, or move your load. When considering the stroke of a cylinder, you should keep within 80% of the maximum stroke. This helps ensure better stability and damage from sideload.
How much accuracy and control is needed?
Hydraulic cylinders are available in single acting and double-acting configurations. A single-acting cylinder uses hydraulic pressure to extend the plunger and a return spring to bring it back to the original position. A double-acting cylinder uses hydraulic force to both lift and lower the plunger. This provides much more control and precision.
How heavy is the load?
Each hydraulic cylinder is built to lift a certain capacity. There are general-purpose designs, which are your “basic” options, and also high tonnage cylinders that have a capacity of up to 1000 tons. Like cylinder stroke, the 80% rule also applies to tonnage. Manufacturers always list their maximum weight capacity as a safe limit. However, good practice with cylinders encourages users to only go to 80% of the manufacturer’s limit.
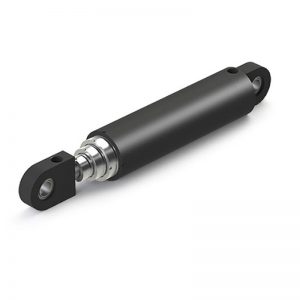